MOULD DESIGN
Mould design
TopWell has a complete range of injection moulding machines which enables us to fulfil the distinct scope of our customers’ stipulation. We have a comprehensive manufacturing set up with flair to design, manufacture & mould contributes to our ability to provide full systems solutions.
Topwell's Engineers use 2D & 3D software to proceed the CAD / CAM processes, we need the 3D drawings for making the mold according to the profile of the parts and the 2D drawings to specify the dimensions & tolerances of the molded parts. Customers can provide ProE Part File; STEP; Parasolid or IGES file format for the 3D part file; and DWG; DXF or SLDDRW file formats for the 2Ddrawings.
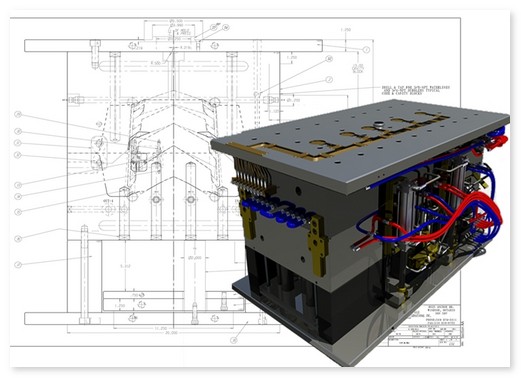
Mold Design Computer Aided Design
Once we receive the Purchase Order from customers, we take immediate actions on two parts, Well-trained 3D Part Engineers use the 2D & 3D software as to:
1.Check the interferences and undercuts of the 3D files; if there is any interference and / or undercut, we instantly inform customer and ask whether they will resend the modified drawing to us or we should modify the part ourselves according to customer's instruction.
2.Define and add the shrinkage rate to the 3D part file.
3.Define the Parting Line of the mold into Cavity Side; Core Side; Slides or lifters; inserts and copper electrodes.
4.Modify the insufficient draft angles for proper ejection of the molded parts; redraw all these parts then send to the CNC Programming section.
5.If the draft angle is not enough for ejection, we usually ask the customer for a larger draft angle then modify the 3D file according to customer's instruction.
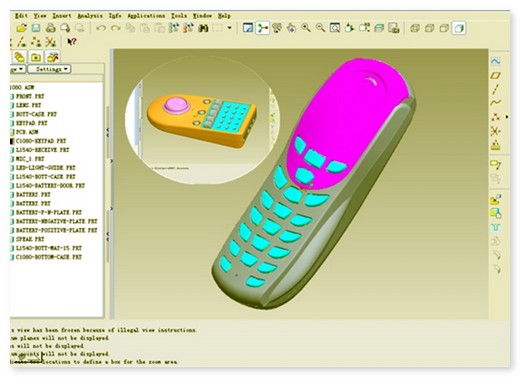
Part Section Analysis
...
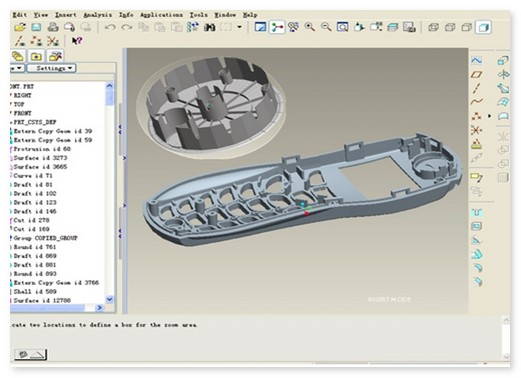
Mold Design Engineers
We usually deeply study the part files from customer then perform our analysis as to:
Ensure that there is no undercut on the part; any interference on mold actions, sufficient draft angle for the surface textures or part ejection.
Design the proper mold actions according to the need. Determine the best injection gate location; best gate type; best gate section area for the part and well balance on the runner for Multi-Cavity mold.
Determine the water cooling and its location, ensure heat transfer is enough that the mold temperature on the Cavity side and Core sides should be as even as possible and make sure that no conservation of heat partially on the cavities or cores.
Make sure that there is enough Air Venting on the mold and for sure no air trap Burn marks when Molding with High Speed.
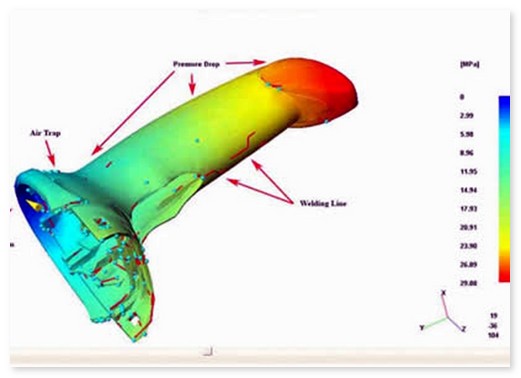
3D Mold Layout
Topwell provides the 3D Mold Layout to the customer if required.
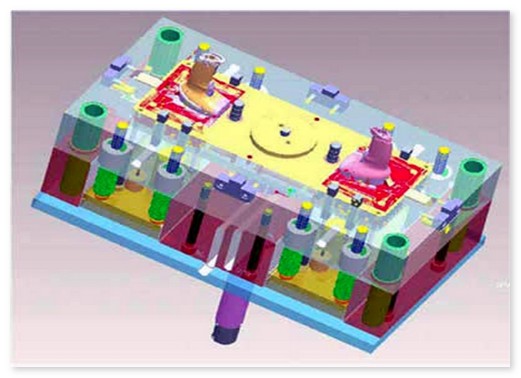
Computer Numeral Control Programming Section
CNC programmers will proceed with the following procedures after receiving the files from the Mold Design Engineers and Parting Engineers:
Compile the CNC programs according to the Modified Part Files.
Perform the tool paths for CNC Milling and / or EDM Wire Cutting, make sure no error or interference exist in the programs.
Send the checked programs via intranet and distribute printed copy to the CNC Machining Section for machining the Steel Inserts or Copper Electrodes. Or send the program via intranet and distribute printed copy to the EDM Wire Cutting Section for EDM Wire Cutting.
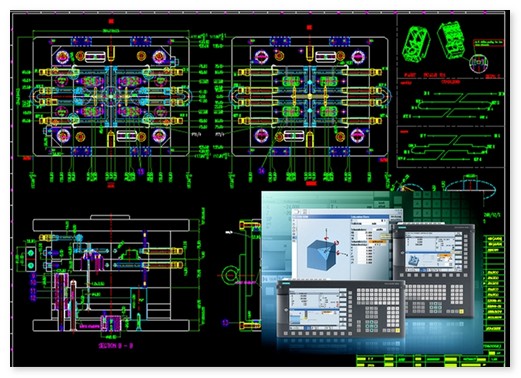
Mold Flow analysis
Topwell Molud design Engineers use Mold Flow for analysis of the gate best position and fill in state. Moldflow provides definitive results for flow, cooling, and warpage along with support for specialized molding processes. We usually conduct Mold Flow to avoid any errors of mold construction and optimised design.
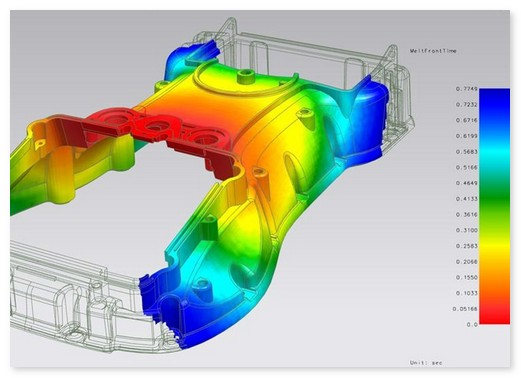